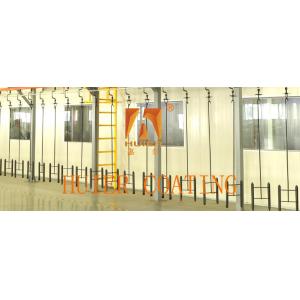
Add to Cart
In addition to powder spraying, paint spraying is another commonly used surface treatment process. This process is to put the paint into a container, pressurize it with a machine, and spray the paint on the product in the form of mist to form a layer of paint film, which protects the product or semi-finished product from rust and corrosion, and serves as a decorative effect. Spray painting is widely used in ships, locomotives, bridges, machinery and other fields.
Before painting, the workpiece must also be cleaned by rust removal, oil removal, water washing, drying and other pre-treatment steps to make the surface clean, so that the paint layer will be more solid. There are two ways to spray paint directly, and there are also two or three times of spraying to obtain a dense and solid paint layer. In the construction of paint, a single layer of coating is rarely used because it does not achieve a uniform and non-porous coating. Usually, a primer layer plus a topcoat layer is used. If necessary, an intermediate layer and a glazing layer outside the closed topcoat layer can be added. The primer layer must have good adhesion to the workpiece to be painted, good bonding to the topcoat layer, and must have anti-rust ability. The matching principles of the primer layer and the topcoat layer are as follows: It is best to match the drying primer layer with the drying topcoat; the self-drying primer with the self-drying topcoat; the primer and topcoat of the same base paint are matched. When using a topcoat with a strong solvent, such as nitrocellulose paint, perchloroethylene paint, etc., the primer layer must be resistant to strong solvents and not be bitten, such as alkyd paint, epoxy paint, etc. The hardness and elongation of the primer and topcoat should be roughly similar. When the active paint is matched with the curing primer, the heat resistance is poor. The oiliness of the primer should be shorter than that of the topcoat, otherwise the weather resistance of the topcoat is poor, and the difference in drying shrinkage between the primer and the topcoat can easily cause cracking of each layer. When using multiple layers of heterogeneous coatings, an intermediate layer is often used to make the paint base transition and achieve a good combination of the base layer and the top layer.
Ferrous metals are suitable for almost all types of primers, while magnesium, aluminum and their alloys usually use passivation primers based on zinc chromate. It is best to conduct effective pretreatment on the surface of the workpiece to form a phosphating film or an oxide film to improve the bonding strength between the substrate and the primer. Then choose a primer with strong adhesion. Primers with red lead pigments must not be used for aluminum and galvanized parts, otherwise it will cause electrochemical reactions and reduce adhesion.